A refinery provides the necessary energy and intermediates for the production of products that are vital to our survival. In order to maintain the flow of the country’s economy, these refineries must run safely.
Millions of individuals may find themselves in problematic circumstances due to supply chain disruptions brought on by outages or accidents.
Human error is one of the main causes of these occurrences, and the best method to decrease it in a refinery environment is by providing all employees and contractors with proper training.
The facility develops a positive safety culture as a result of such training, and everyone collaborates to send everyone home safely each day.
Teaching people to develop the skills they need for their jobs hasn’t altered all that much.Industry 4.0 technologies like Virtual Reality (VR),
Augmented Reality (AR), and Mixed Reality (MR) may completely alter how people learn for the Fourth Industrial Revolution’s emphasis on safety and operational excellence.
Every refinery has safety as a major focus, which is obvious the moment someone walks inside.
To guarantee safe outcomes with regard to individual and process safety, thorough safety procedures, compliance training, and audits are regularly carried out.
The danger of injury increases while operational or maintenance operations are being carried out.
Human brains are already wired to enjoy gambling, and there's evidence that virtual reality is addictive too. What happens when these two powerful entities collide?
DYLAN LOVE Tweet
Upholding strict standards for performance and safety
Several measures are used by businesses to monitor the plant’s safety performance. They keep tabs on the frequency of incidents and near-misses and look into them to determine the underlying causes, get rid of risky behaviours and circumstances, and stop similar incidents from happening again at their facilities.
Injuries are classified when they do occur as recordable injuries that require first aid. Lost-time injuries are a common safety performance statistic used by project organisations and construction firms.
Numerous businesses have accomplished years of injury-free operations, and these measures are also rigorously monitored. It takes a lot of dedication and effort from all employees to produce such outcomes, which are supported by top-notch safety practices and training.
Typical Refinery Training
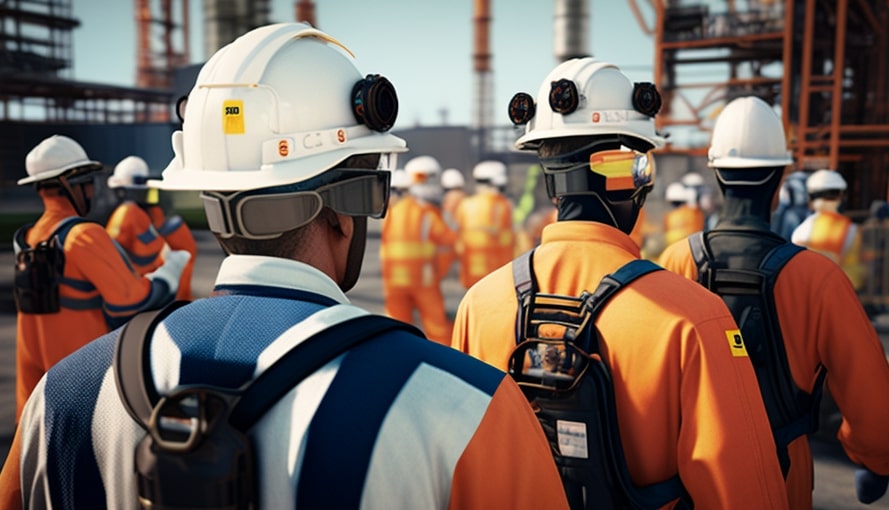
At a refinery, mechanical maintenance work often includes opening equipment, overhauling, removing piping and equipment, doing repairs, and putting everything back in working order.
There is always a chance of physical harm because this is always manual labour done with the aid of machinery.
The majority of this equipment works with extremely dangerous substances that could expose users and harm them.
Hydrogen sulphide and other toxic pollutants are present in crude oil, making it a dangerous substance.
Therefore, it is crucial to assure both the safe completion of the work and the safe return of such equipment to service.
The best-running plants put a lot of attention on achieving this through improved practices and training.
Employee orientation often kicks off refinery training, which goes over crucial safety protocols. Also, they educate staff members about permit to work laws, lockout/tagout procedures, restricted spaces, working at heights, electrical safety, scaffolding, lifting techniques, and other topics.
Training in these methods teaches employees how to conduct tasks correctly and lowers the possibility of accidents and fatalities.
Presentations on slides are always used to offer instruction in classroom settings. The majority of the information is in the form of text, with the odd video and some illustrations to illustrate the key ideas behind these operations.
Despite the fact that the information presented is helpful, the way it was delivered was boring.
If there is any practical training, it often consists of a few exercises that are done in groups to save time. It is not possible to guarantee that each person understands every topic through practice.
Such exercises cannot be performed in a real-world plant environment because doing so would interfere with normal operations and could result in injuries.
While traditional training methods guarantee the participants’ safety, they frequently fail to impart the knowledge and skills required.
Workers frequently learn it only during their on-the-job training or whenever the process units go through turnarounds and maintenance outages.
Few people present that day at the refinery had access to the ability to observe the internals, its arrangement, and the state of equipment after years of operation.
How VR training can be useful?
A specifically made headset is used to immerse the user in a computer-generated 3D environment called virtual reality. This environment can be created to look extremely realistic, and it frequently deceives people into thinking that it is actually a part of the virtual environment.
Virtual reality has pushed suspension of disbelief to new heights.
BRAD BOURQUE
Tweet
The atmosphere of the refinery, including all of its numerous pieces of machinery, pipelines, valves, instruments, and structural components, is created in 3D and is intended to seem extremely realistic thanks to the necessary lighting, texture, physics simulations, etc.
Imagine being able to roam around and see everything around you in a virtual plant ecosystem. Such capacity enables the user to carry out any type of task generally carried out by any function in the refinery environment.
A plant operator, manager, technician, or member of the emergency response team could be this person.
Now, it is possible to train employees in a fully virtual plant setting using virtual reality solutions.
This extremely lifelike virtual plant can represent a single unit or the full building. According to the unit’s Standard Operating Procedures, operators can receive training in both core operations and particular responsibilities (SOP).
They can also receive training on maintenance tasks in accordance with the facility’s Standard Maintenance Procedures (SMP).
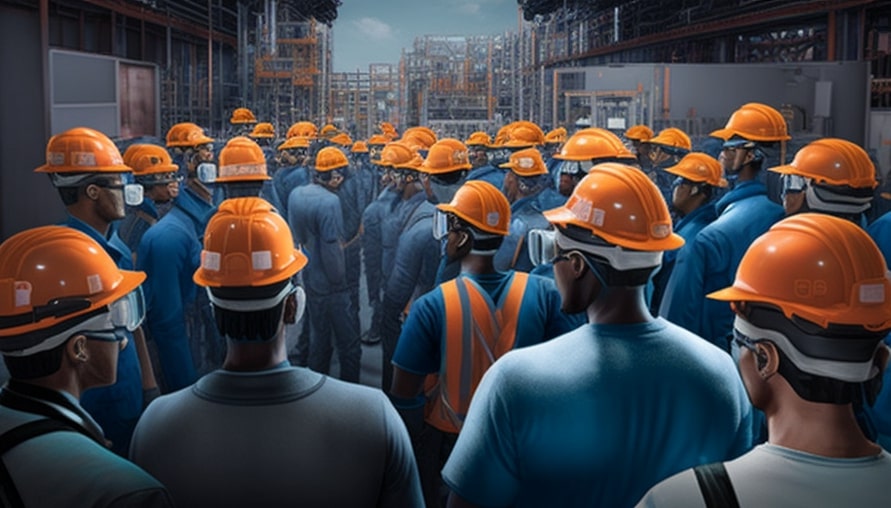
Effective VR Training
The economic advantages of VR in learning and development are highlighted by PWC in its report Seeing is Believing.
They claimed that VR training is 3.75 times more emotionally engaging than other types of instruction and four times faster than conventional classroom training.
By 2030, the sector is anticipated to expand and contribute up to 294 billion dollars to the global economy. That demonstrates the significance of this technology and the scope of VR’s economic opportunities.
Projects to integrate virtual reality training for operations, maintenance, and safety workers have been started by a number of businesses.